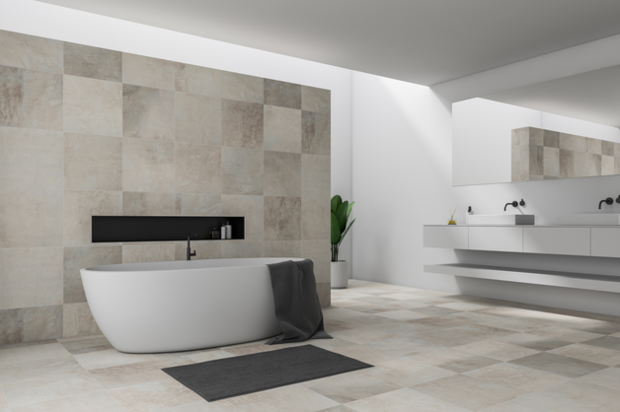
There are screeds based either on cement or on calcium sulphate, i.e. anhydrite. The two materials have a lot in common, but differ fundamentally in some parameters. An anhydrite screed allows fast drying and does not shrink. Cement screed requires slow drying, but in contrast to anhydrite it is also suitable for damp and unventilated areas.
The future use of the room in which the flooring is to be installed is the most important factor in the choice between cement and anhydrite. If permanent humidity is assumed in the room, cement will be a much safer choice, as mature anhydrite must not come into contact with water, otherwise it loses its strength and softens, which can become unpleasantly embedded in the floor covering. You can read more about the application of anhydrite in the bathroom, for example, in a separate text.
Once the screed has been applied, we need to remember the time available and how we can and want to take care of the floor. Although cement screed contains less water during processing, we need to be very careful about the speed of drying. Firstly, it cracks and curls when it dries quickly, and secondly, the rapid drying of cement screed in the early stages can result in its so-called burning, which means that the cement grain will only hydrate superficially or not at all, and the material will not bond (ever!).
Anhydrite, although it contains more water, can dry out (even by force) much faster. If we have underfloor heating in the mix, for example, it is possible to drop it to speed up drying after just seven days. With cement, it is necessary to wait 28 days. On the other hand, if there is no underfloor heating, the anhydrite screed can take a very long time to dry. In the winter months it can take up to six months.
The big difference between cement and anhydrite screeds is mainly in the size of the expansion units (these are smaller parts separated from the whole by expansion joints). In the case of cement screed, each 3 x 3 metre section needs to be dilated
in the case of underfloor heating, and a 6 x 6 metre section where there is no underfloor heating in the composition.
The anhydrite is dilated as a whole. In order to break acoustic bridges, the whole should be one room at a time, with expansion at the door. This allows the transmission of sounds between rooms to be minimised and thus increases acoustic comfort. When the expansion is done correctly, noise transmission is minimised and sound insulation is more effective. However, an anhydrite screed can handle a distance of 200 metres without cracking, which is why, unfortunately, dilatation between rooms is often forgotten in practice. However, breaking the screed (expansion joint) at the threshold also contributes significantly to limiting the spread of noise from room to room.
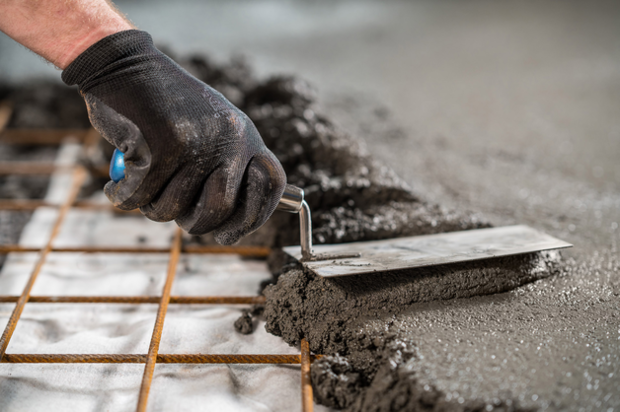
Another difference between cement and anhydrite screeds is the reinforcement.
In cement screeds, a curry mesh reinforcement (a welded mesh made of ribbed reinforcing steel bars) is quite often used, which helps with shrinkage at smaller thicknesses and prevents the screed from cracking as much. Anhydrite, on the other hand, usually does not need reinforcement. If it is necessary for some reason, then a stainless steel reinforcing mesh should be used to prevent corrosion.
Care should also be taken with anhydrite mixtures to avoid contact between the anhydrite
with aluminium. For example, reflective aluminium foils are sometimes used in underfloor heating applications. These must either have a polyethylene film applied from the factory or an additional separation layer must be added between the aluminium and the anhydrite. Otherwise, a chemical reaction will immediately occur between the aluminium and the sulphates in the anhydrite, the reflective aluminium foil will "melt" and, in addition, bubble craters will form on the surface.